1.
The high-voltage connector is composed of: housing (male end, female end), terminal (maleand female terminal), shielding cover, sealing (tail, half end, wire end, contact), protective tail cover, high-voltage interlocking system, CPA system, and other structural components.
2. Standards for high-voltage connectors
High-voltage connectors are currently based on industry standards; there are requirements for safety and performance and testing standards in terms of standards. At present, the most mainstream design of connector manufacturers will refer to the four major European OEMs: Audi, BMW, and Dai. The industry standard LV series standards are jointly developed by Müller and Porsche, while in North America, it mainly comes from its SAEuscar standards. The user itself does not meet draft standards. We often use uscar2, 37, and other related measures, mainly from Chrysler, Ford, and General Motors. EWCAP, a
wire harness connection organization jointly organized by the three major OEMs in the United States, was also mentioned in the online forum. This organization was established in 1994. In 2008, to meet the requirements of more and more HEVs, the organization updated SAE -USCAR 2, which raised the voltage level from the original 20V to the 600V we see now;
For Europe, it was jointly formulated by the European troika (VW BMW Daimler) OEMs. As a car leader, Germany has also played a vital role in developing and promoting its standards. Of course, VW is in related industries. The benefits reflected in the middle have also been demonstrated. For the AK working group, the installation interface size and other requirements have even been refined, which is basically in line with the consistent style of European and American OEMs. TE Amphenol Kostal Molex Delphi and others have also joined these standards. ;
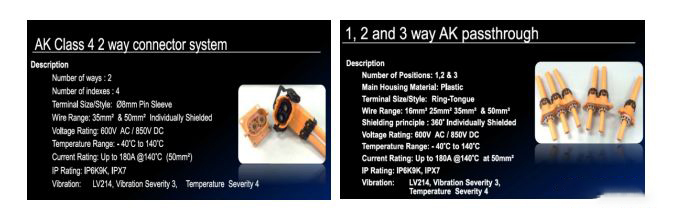
For GB, we have also issued our standards for high-voltage
wiring harnesses and
high-voltage connectors, but in terms of the standard content, many areas need to be further improved and improved so that I won’t go into more details here;
Because high-voltage connectors are generally impossible to appear on vehicles as separate products, they generally need to be equipped with cables, so the standard requirements for their
wiring harnesses are also essential. Generally speaking, there will be more reference to SAE j1742 in the industry;
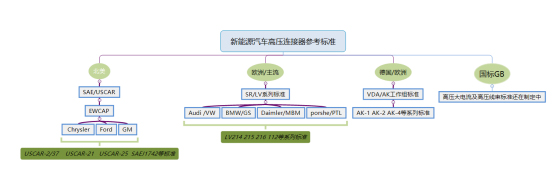
With the development of new energy vehicles to this day, more and more new energy vehicles have come into our lives, whether it is extended-range electric vehicles, hybrid electric vehicles, fuel cell electric vehicles, hydrogen engine vehicles, pure electric vehicles, or other new energy vehicles Etc., a large number of connectors are required. Unlike traditional fuel vehicles, electric cars often have a higher voltage and current platform. Therefore, new energy vehicles often have a large number of high-voltage connectors, purely from the perspective of the connector itself. , Connectors have many classification types: for example, there are circular, rectangular, etc. from the shape, and there are also high-frequency and low-frequency in terms of frequency. Different industries will also be various. We will not expand the description today. Do some sharing for the high-voltage connectors of new energy vehicles;
We can often see a variety of high-voltage connectors on the whole vehicle. Among them, according to the different
wiring harness connection methods, we divide them into two categories of connections:
One is a fixed type that is directly connected by bolts;
One is plug-in connection;
Bolt connection is a kind of connection that we often see on the whole vehicle. The advantage of this method is its connection reliability. The mechanical force of the bolt can resist the impact of automobile-level vibration, and its cost is relatively low. Of course, Its inconvenience is that the bolt connection requires a certain amount of operation and installation space. As the area becomes more platform-oriented and the interior space is reasonable, it is impossible to leave too much installation space. From batch operation and after-sale, it is not suitable from the perspective of maintenance. The more bolts, the greater the risk of human error, so it also has certain limitations; we often see similar products on early Japanese-US hybrid models, of course, now in some passenger cars. We can still see many parallel connections in the three-phase motor cable of the vehicle and the battery power input and output cables of some commercial vehicles. This type of connection generally requires the use of an external box to achieve protection and other functional requirements, so whether to use this method needs to be combined with after-sales requirements from the perspective of the design and layout of the power line of the entire vehicle;
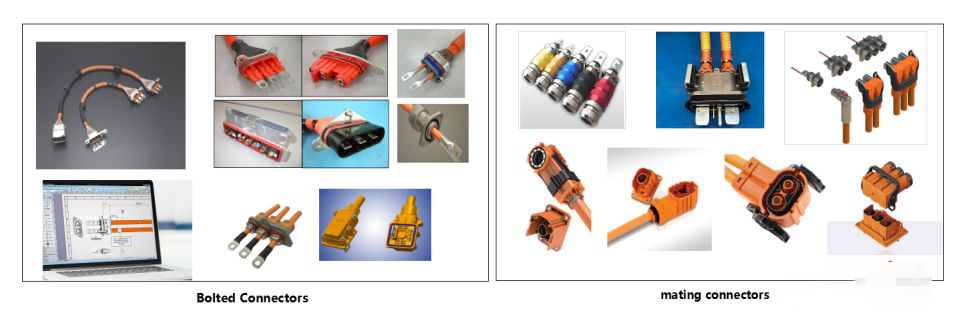
In contrast, the plug-in connector ensures the safety of the electrical connection by connecting two terminal shells, thereby providing a relationship with the wiring harness. Because the plug-in contact can be directly plugged in manually, from a particular perspective, it can still reduce the use of space, especially in some small operating areas;
The plug-in connection also increases as the cross-sectional area of the cable increases and the current increases simultaneously.
From the early direct contact between the male and female ends, it has transitioned to contacting elastic conductors in the middle. The contact method with flexible conductors in the middle is more suitable for more extensive current connections. Its better conductive materials and better flexible design structure are also conducive to Reducing the contact resistance, thereby making the connection of high current more reliable.
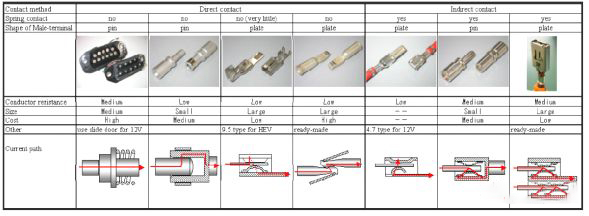
In contrast, the plug-in connector ensures the safety of the electrical connection by connecting two terminal shells, thereby providing a relationship with
the wiring harness. Because the plug-in contact can be directly plugged in manually, from a particular perspective, it can still reduce the use of space, especially in some small operating areas;
The plug-in connection also increases as the cross-sectional area of the cable increases and the current increases simultaneously.
The early direct contact between the male and female ends has transitioned to contacting elastic conductors in the middle. The contact method with flexible conductors in the middle is more suitable for more extensive current connections. Its better conductive materials and better flexible design structure are also conducive to Reducing the contact resistance, thereby making the connection of high current more reliable.