Before the
high-voltage cable harness space arrangement, the location of the equipment end on the whole vehicle has usually been determined. The high-voltage harness arrangement, combined with the vehicle 3D data proper wiring, should pay attention to the protection of high-voltage harness, fixed and concealed. This article introduces the main points of high-voltage cable assembly. The following is the text.
In general, three key factors decide the assembly quality.
Firstly, the mating: connectors and pins mating, connectors to connectors mating, cables and connectors mating and the connectors to sockets mating
Second, the connectors. For High-volt connector, we usuall choose Molex high-volt series such as MOLEX 33472-1206 MX150 Sealed Female Connector, Deutsch Connectors HV series such as, Aptiv HV series such as 12065863,12047937 DELPHI 15326654, 12065158 ;
AMPHENOL series like AT04-12PA-PM12. And in battery cable, Anderson Connectors such as SB50, SB120, SB175, SB350 are widely applied;
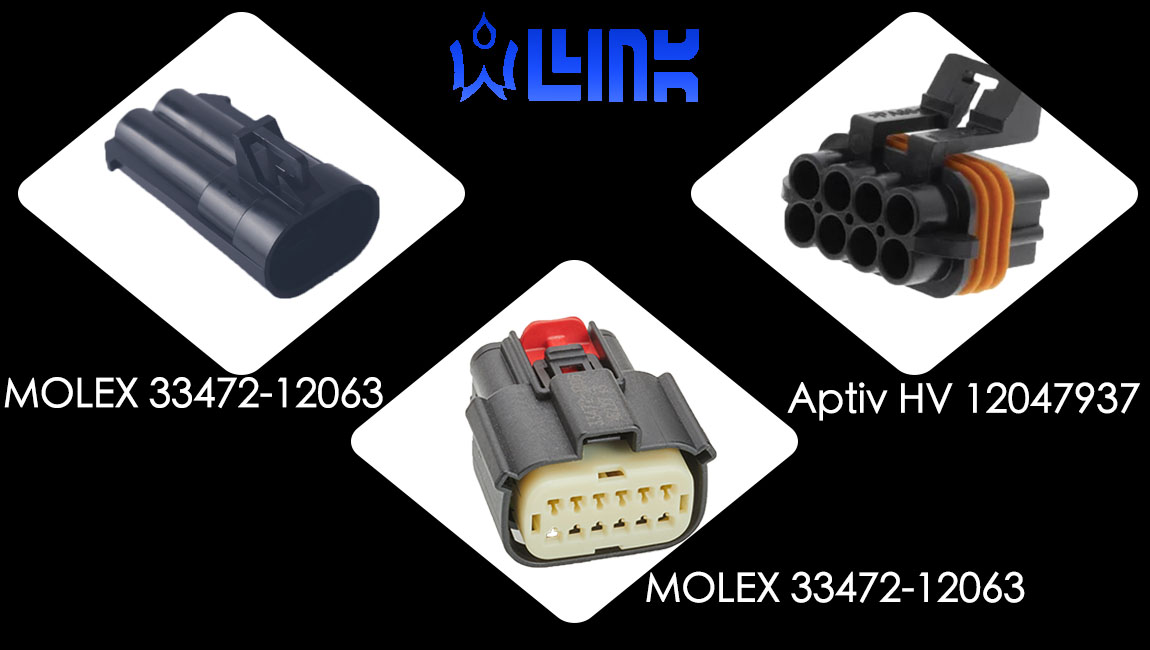
In some cases, we will also using M21 circular waterproof connectors for solar PV panel, esp. For Solar to EV chargers. EV charging gun is an exception.
Third, the layout. A scientific layout save both money and energy.
The arrangement of high-voltage equipment and the arrangement of the
wiring harness are also related and need to be considered mutually. The layout of the program is not determined by unilateral locking.
Basic principles of HV harness space arrangement.
Suppose the HV cable assemblies needs to be connected to the front and luggage compartments due to design requirements. In that case, the HV cable harness can be routed under the vehicle chassis through the body sheet metal holes, which is also beneficial to the EMC design of the HV wiring harness.
Avoid running the wires together with the low-voltage harness to prevent interference with the low-voltage wire harness;
High and low-voltage harnesses should avoid cross-wiring as far as possible. High and low voltage harnesses parallel wiring 100mm apart (unless it does not affect EMC)
The high voltage harness should be at least 100mm away from the fuel line.
The distance between the associated positive and negative wires should be maintained at 20mm (measured by the distance between the outer edges of the shield).
The length difference between the associated wires must not exceed 35mm.
At least 10mm clearance between the high voltage harness and the stationary parts.
High-voltage harness and moving parts distance at least 25mm; (motion envelope)
It should try to avoid the body collision deformation of the larger area, to prevent the vehicle after the accidental collision of high-voltage cable are cut by the sheet metal or insulation layer is destroyed, resulting in the body with high voltage to form electric shock injury, such as not happen in the front and rear crash beam, side panel, and door alignment as far as possible.
2, the associated high-voltage harness (such as motor three-phase line or main power battery pack line) must be unified together and symmetrically arranged.
3、The cable harness should be protected and fixed during the space arrangement.
4, the wire harness bending radius should not be too small. Too small will cause connector seal failure, wire insulation damage. The following table shows the appropriate bending radius of the wire.
Note: The outer diameter refers to the outermost insulation skin diameter; some manufacturers of high-voltage cable bending radius can be less than the above table requirements, the need to determine with the supplier its bending radius and testing requirements and methods.
5. For Wire harness in the body sheet metal hole, you need to use the rubber sleeve over the hole protection and sealing, and in the hole before and after the wire harness is fixed.
6. Plug-in arrangement
The process needs to consider the operating space of the connector, usually in the layout process, in CATIA and other 3D software simulations, to determine whether there is plugging and unplugging room.
The operating space needs to consider the distance generated by the rotation or flat movement of some parts during the disassembly and installation of the connector, as shown below for the HV2000 connector space dimensions.