As an expert manufacturer of
wire harness processing, we've got summarized some points for attention in
wire harness and
cable assembly processing for your reference supported years of industry experience.
Not matter we are making simple single
wire or cable processing or complicated
wiring looms, or high quality
HSD LVDS cable assembly, we need to apply our strict rule in IPC620 and WWHA members standard work guidance in our processing.
There are millions of different looks of
wiring harness, but all of them are made by similar
wires and cables procession, that craft make it different.
Let’s say it one by one.
1. Wire cutting: check whether the quality style of the wire is correct, whether the dimensions meet the requirements; the cutting must be flush, the wire can not be scratched, and also the wire isn't dirty.
2. Stripping: Check whether the stripping end is flat, sharp cut, braid organizing etc., and also if the stripping scale is correct.
3. Strip ends treatment: is that the trimming scale correct? Is that the trimming in even? The core wire shouldn't be damaged when trimming and organizing .
4. Stripping the insulation: check whether the stripping end is even; whether the stripping scale is correct; whether the core wire is stripped or the copper wire is broken; the insulator cannot fall when it's half-stripped.
5. Set shortening tube: check whether the dimensions and kind of shortening tube are correct.
6.Prepare soldering tin: Check whether the temperature of the tin furnace is correct; whether the core copper wire is arranged before preparing for soldering, whether there are signs of bifurcation, twists, and discounts; whether there's a copper wire bifurcation after preparing the soldering tin, the looks of a giant head, uneven copper wire, and burned insulation.
Below is some
wire harness we built for car radio, car light and car led light kits
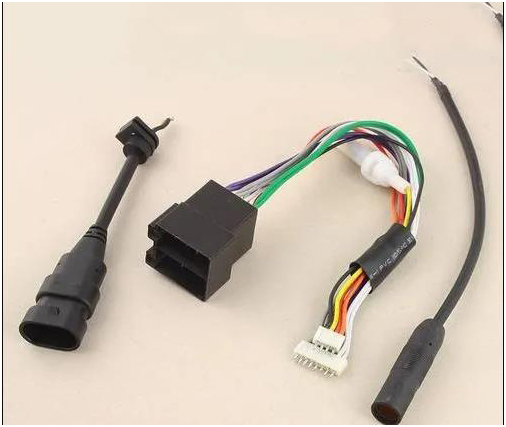
7. Soldering tin: Check whether the temperature of the electrical hand tool is correct; the insulation mustn't be burnt, the tin point should be lubricated, and there should be no tin tip, no false soldering or virtual soldering.
8.
Terminal and pins crimping:
pins crimping is critical control point for a
cable harness set or cable assembly. We should acknowledge whether the standards of terminals and wires are correct; whether the crimping of the airport includes a bell mouth, skew, insulation and core wires are too long or too short.
9.
Pins and contacts piercing: Check whether the connector and terminal type are correct, whether the terminal is broken or deformed, whether the airport is missing, incorrectly inserted, or not pierced in situ.
10.Crimping of the
cable: Check whether the sort of connector is correct; whether the direction of the road is right; whether the core wire is broken, exposed copper, or scalded; whether the crimping is in situ.
11.Blow shortening the tube: is that the shortening of the road outstanding and can't burn the insulation.
12. Assembled to the
connector: is that the body incorrectly installed, whether there are scratches, burrs, etc., whether there are missing parts, whether the screws are unscrewed, oxidized, discoloured, loose, etc., and there's no lousy conformity after assembly; if the
connector is with pin nos. Showing orientation, then it must be assembled consistent with requirements.
13.Labeling: Check whether the content of the label is correct, precise, and without hyphenation; whether the size of the title is accurate; whether the brand is dirty or damaged; whether the orientation of the label is correct.
14.Tie the tie: check whether the quality, colour and orientation of the fastener are correct; there's no sign of cracking or looseness.
15.
Injection moulding: check whether there's dirt on the mould, whether there's a cloth shortage, air bubbles, poor bonding, insufficient hardening, etc., within the moulding part.
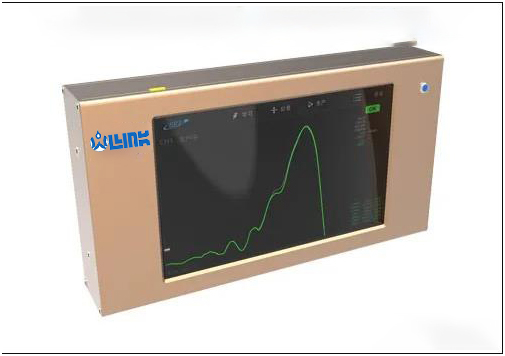
16.Plug moulding: Check the plug moulding for damage, unevenness, lack of fabric, burrs, debris, flow lines, etc., and admit that the metal terminals haven't any defects like deformation, damage, and copper exposure.
17.Electrical inspection: Check-in step with the wants of the inspection guide ticket of the related product.
18.Appearance check: It should be noted that as long because it is visible, all items must be checked.
Packing and warehousing should be reasonably packed and stored for every
wire harness. Otherwise, the qualified products will become defective products, which is additionally vital.