What are the most important factors to consider about when choosing pins,contacts and terminal blocks for a custom wire harness or cable assembly?
The pins, contacts and terminal block may be a suitable accessory product accustomed to realize the electrical connection, divided into the connector category within the industry. It's a chunk of metal-enclosed in insulating plastic. There are holes at both ends to insert the wires. There are screws for fastening or loosening. For instance, two wires must be connected sometimes, and sometimes they have to be disconnected. They'll be related to terminals and might be disconnected without having to weld them or twist them together, which is incredibly convenient and quick. And it's suitable for an excessive number of wire interconnections. There are special terminal blocks and terminal boxes within the wattage industry, all of which are connected terminals, single-layer, double-layer, current, voltage, ordinary, breakable, and so on. a particular crimping area is to confirm reliable contact and to make sure that sufficient current can pass.
When choosing terminal blocks, the subsequent factors should be considered:
1. Power factor
The power factor mainly considers as this, voltage, and power of the terminal. Per the load current and voltage, choose the corresponding level and leave the space for the port.
2. Wire size/wire gauge
For different wiring terminals, their size and wiring range are diverse. Generally, when using terminals, it's better to settle on a wiring range that's slightly larger than the particular wire diameter. Because the current market standards are somewhat chaotic if you choose a wiring aperture of the identical size because of the wire diameter, you'll not be ready to insert the wire into the crimping frame because the terminal produced within the market doesn't meet the quality, leading to a smaller wiring range. So choosing standard terminals for standard wire is very important for golf cart wire harness and waterproof cable assembly
3. the number of space used
Different terminals are selected for various space sizes. For instance, during a small space, you'll choose a double-layer terminal or a three-layer terminal.
4. Environmental factors
Environmental factors mainly consider the convenience of the operator and also the ecological requirements of the equipment itself. Convenient operation, reduced labour intensity, and improved work efficiency are the desires that everybody pursues. For the environment where the equipment is found, like whether the vibration frequency is just too large, whether the dust is just too large, etc., you'll choose the corresponding terminal combination.
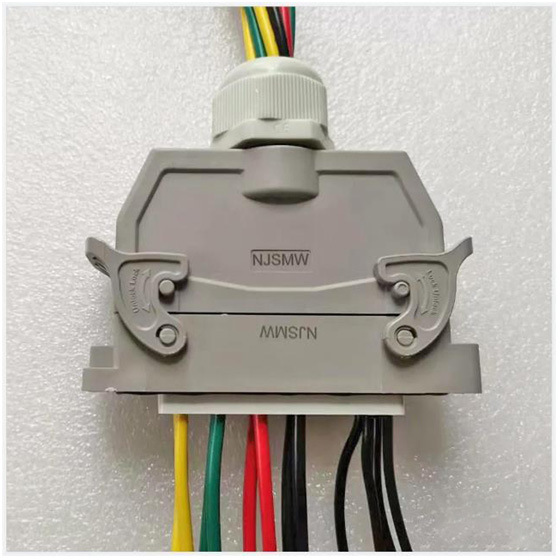
Guess what application is this wire harness for with above strange connector
What is the idea for the proper selection of wiring terminals?
The terminal block may be a reasonably accessory product accustomed to realize the electrical connection, which is split into the category of the connector within the industry. It's actually a chunk of metal-enclosed in insulating plastic. There are holes at both ends to insert the wires. There are screws for fastening or loosening. As an example, two wires must be connected sometimes, and sometimes they have to be disconnected. They'll be related to terminals and may be disconnected at any time without having to weld them or twist them together, which is highly convenient and quick. And it's suitable for a large number of wire interconnections. Within the electrical power industry, there are special terminal blocks and terminal boxes, all of which are connected terminals, single-layer, double-layer, current, voltage, ordinary, breakable, and so on. a selected crimping area is to make sure reliable contact and to confirm that sufficient current can pass.
You should also listen to the following points when purchasing wiring terminals:
1. Appearance, good look is also important even for connectors and pins. Nowadays, HSD LVDS connectors almost look like an artwork instead of industry pieces.
A suitable terminal should first have good artistry, and if it fails the visual inspection, there's basically no must waste time conducting electrical tests. So, what quite terminal block is taken into account good artistry? The industry generally believes that qualified plastic parts for terminal blocks should don't have any deformation, flat surface, no scratches, no burrs at the corners, and uniform wall thickness; more importantly, the plug and also the pin seat has a high fit, and there's no excessive insertion force. And also, the phenomenon of too low appears.
2. Material, which is always key on good quality wiring looms and wire harnesses
The first is that the plastic parts, which must have good flame retardancy, that is, the flame retardant grade of UL94V-0; the straightforward test method is to ignite an open flame, and therefore the plastic parts leave the open flame to extinguish, which suggests that the terminal has good flame retardant performance; Wire crimping frame, the wire crimping frame that a lot of customers often say about whether the airport is created of copper or not actually refers to the crimping structure. Carefully recognizing from the looks, the copper frame contains a more angular texture than the ore. Of course, the safest way is to disassemble the plastic part and eliminate the crimping edge for further inspection. You can not hear the words of the salesperson.
3. Torque
90% of the poor contact of the terminals on the market is thanks to the screw torque that can't meet the wants. Therefore, the screw torque of the airport is crucial. Consequently, it's best to personally use a screwdriver to feel whether the screw can press the wire tightly.
How to prevent impurities from entering the injection moulding machine during the assembly of terminal blocks
The production of terminal blocks is mainly divided into two parts: injection moulding production and copper production. Finished products are often produced when the parts are assembled. The necessities of injection moulding production are more stringent than the assembly of copper parts because the non-standard production process will cause insulation. The components have a significant impact on strength and insulation.
The first is about the fabric of plastic parts. High-quality materials have good insulation, excellent toughness, and flame retardancy. The way to mix impurities within the material will affect the strength and various properties of the merchandise, especially metal powder can not be combined, which can cause the merchandise shell to conduct electricity and cause installation accidents, and also the metal powder can enter the following ways.
The first is that the second-use plastic parts that are crushed after the disassembly of the unqualified product. They'll hesitate to disassemble incompletely and leave metal parts. When passing through the crusher, the metal parts are crushed to create a metal powder. When using the cycle, the metal powder passes through the injection moulding machine. It's mixed into plastic parts.
Metal powder mixed in raw materials and metal powder combined with non-original materials also are a significant hidden danger within the production of plastic parts, so you would like to use caution when buying materials.
The additives within the granulation material will cause the plastic parts to be unqualified because the raw materials utilized in the granulation don't seem to be known by ordinary manufacturers, and also the additives added also are not known.
Therefore, a powerful magnet is often added to the barrel within the injection moulding process, which might effectively solve the inhalation of most of the metal, and also, the original material should be selected the maximum amount as possible for the acquisition of raw materials.
Terminal plating trend
The electroplating of the metal parts of the terminal is that the basic standard of the industry, and also the products of various levels: the electroplating method and therefore the coating metal are different-the higher the wants, the higher the standard of the products, the electroplating is more environmentally friendly and scientific. With the event of your time, the electroplating I art is additionally more perfect.
The function of electroplating lies within the appearance of the merchandise and also the improvement of the corrosion resistance of the merchandise. At an identical time, the high-quality plated metal may also reduce the electrical resistivity of the wiring and improve the product's performance. Of course, electroplating is harmful to the environment; hefty metals are very toxic to the environment and therefore the flesh, so with the event of society, more and more attention is paid to environmental protection, and plenty of electroplating that's harmful to the environment has been abandoned.
Commonly used electroplating processes within the terminal industry are multicoloured, galvanized, nickel-plated, silver-plated, gold-plated, and so on. Within the current market, the electroplating process is gradually eliminated because it's more harmful to the environment. Within the past, most of the SAK series terminals were produced by electroplating multicoloured technology, which is characterized by cheap processing, which could be a very cost-effective processing technology for low-end products.
In the past, small and secret electroplating workshops were sealed up. Under strict monitoring, the electroplating process of the products has been improved. This is often the trend of industry development over the years.
Good quality custom wire harness and cable assembly is depends on craft man, good machine,qualified materials and good environment, Olinktek worked it on for past 20 years and still keen on it.